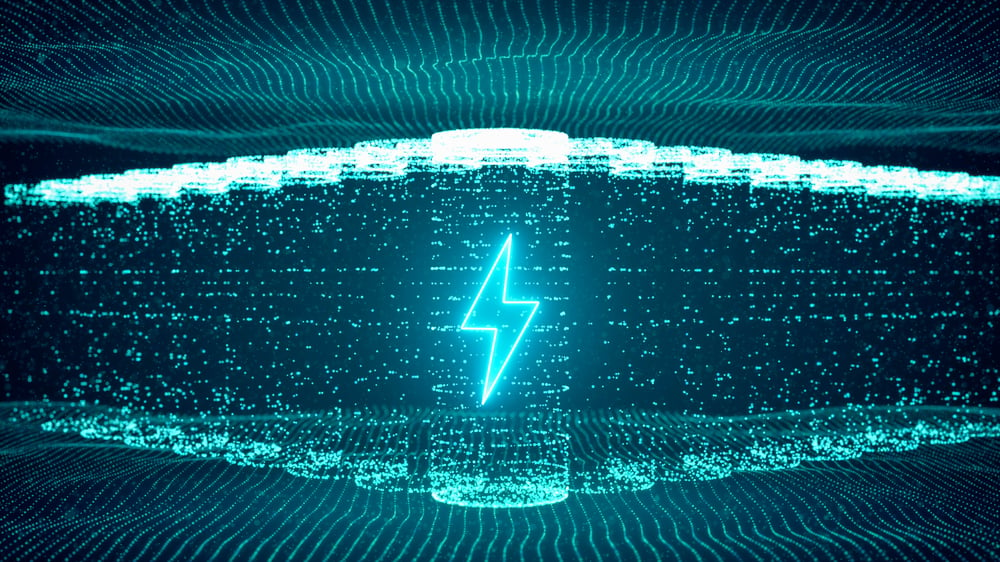
The future of resources in the battery industry - ECO STOR and the circular economic perspective

Raw materials like lithium and cobalt are finite natural resources, and their extraction has been leaving a big carbon footprint and making a huge impact on the local landscape and human resources. With the ever-growing demand for lithium-ion batteries for consumer electronics and electric vehicles, one should think that the green transition is not that green after all, and that supply cannot meet demand. But a powerful global sustainment strategy, and the onset of new technology and chemistry, should be leading the development in a positive direction.
The race toward climate neutrality
Becoming carbon-free in a sustainable and profitable way requires a shift from fossil-fueled energy to energy from renewable sources like sun, wind, and water, combined with large-capacity battery energy storage systems and a well-developed power grid infrastructure.
Industrial countries are already several steps ahead of developing countries in this race, having the economic resources to invest in both necessary research and the very solutions for renewable energy usage. Ironically, developing countries are more affected by the negative climate changes, caused by the greenhouse gas emissions from burning fossil fuels. And they can’t do much about it.
That’s why rich, industrial countries like Norway have a greater responsibility to work for a more sustainable economy with renewable energy and careful management of our natural resources.
A circular economy
Ellen MacArthur, the British sailor and founder of The Ellen MacArthur Foundation, says that «we have finite resources available to us once in the history of humanity, yet our economic model uses them up». And that is the naked truth. Regardless of greenhouse gas emissions from fossil-based energy or battery energy storage. Given also the accelerated speed of electrification development, it is more important than ever to find ways to recycle our resources and create a circular economy.
According to MacArthur, design, technology and chemistry are key factors. At the start of every single product being made, we have to think that this material needs to be fed back into the economy. Such a system also requires the infrastructure for recycling to be fully functioning. Additionally, we have to look at some of today's waste as resources instead. And all players have to work together, meaning everyone from the finance industry to the marketing industry and the managers within organisations.
Read more: Four ways ECO STOR makes the EV battery-industry part of the circular economy
Lithium – the «white gold»
The element lithium has, in contrast to common knowledge, abundant occurrence on earth. Not as a pure metal, but as a very reactive material concentrated in salt-lake brines or in hard rocks or crystals, so-called spodumene. The biggest spodumene ever found was 15 m long and weighed 10 tons.
The mine extraction and further processing of the silver-white and light-weight element, however, is concentrated in a few countries, with Australia, Chile, and China as the top three. And the mining industry has traditionally been operating in a conservative and ruthless manner, whilst destroying natural resources and exploiting cheap and accessible workforce, including child labour.
Fortunately, the system is already starting to change, as the world market’s focus on transparency in environmental, social, and governance factors (ESG) increases, and the ever-evolving technology allows us to handle our natural resources more carefully and efficiently. New extraction methods can save the environment from both excessive water usage and the need for large areas for the brines.
The increasing global demand for lithium, which is the main material in lithium-ion batteries for both consumer electronics and EVs, makes more countries eager to join the game in search of the “white gold”. Not only by establishing lithium mines, but also lithium processing plants, in order to complete and strengthen the supply chain and become less independent of other countries. And new lithium reserves are being discovered as we speak, to both excitement and frustration, as more mining means fewer resources.
Read more: Why does battery energy storage play a crucial role when energy systems change
Urban mining: recycling the lithium
Forecasting the future supply of lithium is a simple calculation, taking into consideration the extreme increase in demand we are experiencing now. And it doesn’t take a rocket scientist to figure out that we have few options if the increasing requirement for lithium for all our electronic devices continues.
Perhaps research and science will give us a completely different situation in time, with new and groundbreaking battery technology and the use of other raw materials, but for now, we expect lithium to stay with us through the automotive transition.
That brings us to urban mining – one of the options we actually do have. Urban mining is the retrieving of metals through recycling instead of extraction. Lithium and cobalt can be chemically extracted from shredded battery cells, using the same method as in mining, and then purified through a hydrometallurgical process. This way we can recover all valuable metals from spent lithium-ion batteries, instead of mining new ones.
Metal refining has until recently been an energy-intensive process, but new chemistry and technological tools now allow us to execute it more sustainably and cost-effectively than before.
The result? A significant and much-needed pressure relief on the trembling mining industry, and a very important step towards resource circularity and a sustainable future.
What is ECO STOR’s role?
As part of the EV revolution, ECO STOR wants to contribute by making the life cycle of lithium-ion batteries in EVs longer and more sustainable, and there are three main ways to do it.
One is by repairing the batteries, thus giving them a longer life span.
Two is by reusing them for another, but similar purpose, such as in battery energy storage systems.
Three is by recycling them; separating the different metals from each other, bringing them back to the value chain as raw materials.
ECO STOR has predominantly chosen the second way - reusing the batteries for another purpose. We have made beneficial deals with several EV manufacturers, giving us easy access to spent lithium-ion batteries. We implement them in state-of-the-art battery energy storage installations, which enables us to deliver custom-made storage systems for commercial, public, agricultural, and private use.
Investing in battery recycling
In addition, ECO STOR has formed a joint venture, a lithium-ion battery recycling facility, with the Canadian recycling company Li-Cycle and the Norwegian battery cell manufacturer Morrow Batteries. The joint venture is going to be a so-called Spoke facility, in reference to the first mechanical part of the two-step innovative process (Spoke & Hub Technologies™) of recycling lithium-ion batteries, established by Li-Cycle.
The Spoke process includes shredding whole non-discharged and non-dismantled lithium-ion batteries mechanically, adding a neutralising solution, resulting in three different product outcomes; shredded plastics, copper/aluminium foils and “black mass”.
Traditionally, the black mass has been sold back to the battery market for further refining, but in this partnership, the black mass is going back to Li-Cycle, who refines it through the Hub hydrometallurgical process, into valuable materials like lithium carbonate, cobalt sulphate, nickel sulphate and manganese carbonate.
The process enables a resource recovery percentage of up to 95 %, in comparison to the former 50 % recovery rate. And all of this without creating landfill waste, wastewater and air emissions caused by the traditional thermal processing.
The Norwegian Spoke, forecasted to be up and running at the start of 2023, will have the capacity to process up to 10 000 tons of lithium-ion batteries per year, such as battery manufacturing scrap, energy storage systems and full EV packs. The new facility is modular, being created, tested and shipped by Li-Cycles partner, Koch Engineered Solutions.
This joint venture represents a closed-loop battery supply chain comprising the world’s most sustainable and cost-effective battery cell production, innovative battery reuse and hightech battery recycling, all three parts being key players as we move forward in the EV revolution.